Diffusion welding
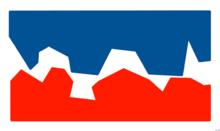
Diffusion welding (DFW) is a solid state welding process by which two metals (which may be dissimilar) can be bonded together. Diffusion involves the migration of atoms across the joint, due to concentration gradients. The two materials are pressed together at an elevated temperature usually between 50 and 70% of the melting point. The pressure is used to relieve the void that may occur due to the different surface topographies. The method was invented by the Soviet scientist N.F. Kazakov in 1953.[1] Specific tooling is made for each welding application to mate the welder to the workpieces.[2]
Applications
DFW is usually used on sheet metal structures. Typical materials that are welded include titanium, beryllium, and zirconium. It is usually used on low volume workpieces mainly for aerospace, nuclear, and electronics industries.
In many military aircraft diffusion bonding will help to allow for the conservation of expensive strategic materials and the reduction of manufacturing costs. Some aircraft have over 100 diffusion-bonded parts, including; fuselages, outboard and inboard actuator fittings, landing gear trunnions, and nacelle frames.
Notes
- ↑ Kazakov, N.F (1985). "Diffusion Bonding of Materials". Pergamon Press.
- ↑ http://www.welding-advisers.com/Diffusion-welding.html
Further reading
- Kalpakjian, Serope, Schmid, Steven R. "Manufacturing Engineering and Technology, Fifth Edition", pp. 771-772
External links
- "Cast Nonferrous: Solid State Welding," at Key to Metals
- An excellent discussion of diffusion bonding by Amir Shirzadi for the UK Centre for Materials Education