Pig iron
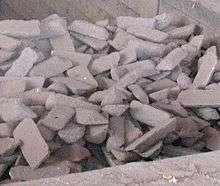
Pig iron is the intermediate product of smelting iron ore. It is the molten iron from the blast furnace, which is a large and cylinder-shaped furnace charged with iron ore, coke, and limestone. Charcoal and anthracite have also been used as fuel. Pig iron has a very high carbon content, typically 3.5–4.5%,[1] along with silica and other constituents of dross, which makes it very brittle and not useful directly as a material except for limited applications.
The traditional shape of the molds used for pig iron ingots was a branching structure formed in sand, with many individual ingots at right angles[2] to a central channel or runner, resembling a litter of piglets being suckled by a sow. When the metal had cooled and hardened, the smaller ingots (the pigs) were simply broken from the runner (the sow), hence the name pig iron.[3] As pig iron is intended for remelting, the uneven size of the ingots and the inclusion of small amounts of sand caused only insignificant problems considering the ease of casting and handling them.
History
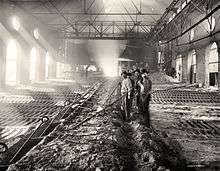
Smelting and producing pig iron and other iron products was known to the Ancient Egyptians and gradually spread around the Eastern Mediterranean as far as Ancient Greece.[4] The Roman Empire and later the Muslim caliphates of the Middle Ages inherited and refined these technologies. Because of the collapse of the Western Roman Empire, Western Europe did not rediscover the process until the Late Middle Ages (1325–1500).[5] The phase transition of the iron into liquid in the furnace was an avoided phenomenon, as decarburizing the pig iron into steel was an extremely tedious process using medieval technology.
The Chinese were also making pig iron by the later Zhou Dynasty (which ended in 256 BC).[6]
Uses
Traditionally pig iron was worked into wrought iron in finery forges, later puddling furnaces, and more recently into steel.[7] In these processes, pig iron is melted and a strong current of air is directed over it while it is stirred or agitated. This causes the dissolved impurities (such as silicon) to be thoroughly oxidized. An intermediate product of puddling is known as refined pig iron, finers metal, or refined iron.[8]
Pig iron can also be used to produce gray iron. This is achieved by remelting pig iron, often along with substantial quantities of steel and scrap iron, removing undesirable contaminants, adding alloys, and adjusting the carbon content. Some pig iron grades are suitable for producing ductile iron. These are high purity pig irons and depending on the grade of ductile iron being produced these pig irons may be low in the elements silicon, manganese, sulfur and phosphorus. These types of pig irons are used to dilute all the elements in a ductile iron charge (except carbon) which may be harmful to the ductile iron process.
Modern uses
Until recently, pig iron/slag was typically poured directly out of the bottom of the blast furnace through a trough into a ladle car for transfer to the steel mill in mostly liquid form; in this state, the pig iron was referred to as hot metal. The hot metal was then poured into a steelmaking vessel to produce steel, typically an electric arc furnace, induction furnace or basic oxygen furnace, where the excess carbon is burned off and the alloy composition controlled. Earlier processes for this included the finery forge, the puddling furnace, the Bessemer process, and the open hearth furnace.
Modern steel mills and direct-reduction iron plants transfer the molten iron to a ladle for immediate use in the steel making furnaces or cast it into pigs on a pig-casting machine for reuse or resale. Modern pig casting machines produce stick pigs, which break into smaller 4–10 kg piglets at discharge.
See also
References
- ↑ Camp, James McIntyre; Francis, Charles Blaine (1920). The Making, Shaping and Treating of Steel (2nd ed.). Pittsburgh: Carnegie Steel Co. p. 174. OCLC 2566055.
- ↑ Glossary of Metalworking Terms. Industrial Press. 2003. p. 297.
- ↑ The Making, Shaping, and Treating of Steel: Ironmaking volume (PDF). AISE Steel Foundation. 1999. p. 18.
- ↑ Waldbaum, Jane C. From Bronze to Iron. Göteburg: Paul Astöms Förlag (1978): 56–58.
- ↑ Several papers in The importance of ironmaking: technical innovation and social change: papers presented at the Norberg Conference, May 1995 ed. Gert Magnusson (Jernkontorets Berghistoriska Utskott H58, 1995), 143-179.
- ↑ Wagner, Donald. Iron and Steel in Ancient China. Leiden 1996: Brill Publishers
- ↑ R. F. Tylecote, A history of metallurgy (2nd edition, Institute of Materials, London, 1992).
- ↑ Rajput, R.K. (2000). Engineering Materials. S. Chand. p. 223. ISBN 81-219-1960-6.
![]() |
Wikimedia Commons has media related to Pig iron. |