X-ray tube
An X-ray tube is a vacuum tube that converts electrical input power into X-rays.[1] X-ray tubes evolved from experimental Crookes tubes with which X-rays were first discovered on November 8, 1895, by the German physicist Wilhelm Conrad Röntgen. The availability of this controllable source of X-rays created the field of radiography, the imaging of partly opaque objects with penetrating radiation. In contrast to other sources of ionizing radiation, X-rays are only produced as long as the X-ray tube is energized. X-ray tubes are also used in CT scanners, airport luggage scanners, X-ray crystallography, material and structure analysis, and for industrial inspection.
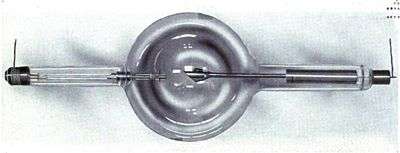
Types
Rotating anode tube

- A: Anode
- C: cathode
- T: Anode target
- W: X-ray window
.jpg)
The anode is supported on vacuum bearings and can be rotated by electromagnetic induction from a series of stator windings outside the evacuated tube. Typically, eddy currents are induced in a rotatable metal cylinder, the rotor. The superimposition of external magnetic induction and induction from the eddy currents, which changes direction with time, creates a driving mechanical momentum in the rotor.
Because the entire anode assembly has to be contained within the evacuated tube, heat removal is a serious problem, further exacerbated by the higher power rating available. Due to the high heat generation, a matched thermal expansion of glass and the anode material is necessary. For this, high-borate borosilicate glass pioneered by Otto Schott is often used. Direct cooling by conduction or convection, as in the Coolidge tube, is difficult. In most tubes, the anode is suspended on ball bearings with silver powder lubrication which provide almost negligible cooling by conduction.
A recent development has been liquid gallium lubricated fluid dynamic bearings which can withstand very high temperatures without contaminating the tube vacuum. The large bearing contact surface and metal lubricant provide an effective method for conduction of heat from the anode.
The anode must be constructed of high temperature materials. The focal spot temperature can reach 2,500 °C (4,530 °F) during an exposure, and the anode assembly can reach 1,000 °C (1,830 °F) following a series of large exposures. Typical materials are a tungsten-rhenium target on a molybdenum core, backed with graphite. The rhenium makes the tungsten more ductile and resistant to wear from the impact of the electron beams. The molybdenum conducts heat from the target. The graphite provides thermal storage for the anode, and minimizes the rotating mass of the anode.
Increasing demand for high-performance Computed tomography (CT) scanning and angiography systems has driven development of very high performance medical X-ray tubes. Contemporary CT tubes have power ratings of up to 100 kW and anode heat capacity of 6 MJ, yet retain an effective focal spot area of less than 1 mm2.
Microfocus X-ray tube
Some X-ray examinations (such as, e.g., non-destructive testing and 3-D microtomography) need very high-resolution images and therefore require X-ray tubes that can generate very small focal spot sizes, typically below 50 µm in diameter. These tubes are called microfocus X-ray tubes.
There are two basic types of microfocus X-ray tubes: solid-anode tubes and metal-jet-anode tubes.
Solid-anode microfocus X-ray tubes are in principle very similar to the Coolidge tube, but with the important distinction that care has been taken to be able to focus the electron beam into a very small spot on the anode. Many microfocus X-ray sources operate with focus spots in the range 5-20 µm, but in the extreme cases spots smaller than 1 µm may be produced.
The major drawback of solid-anode microfocus X-ray tubes is the very low power they operate at. In order to avoid melting of the anode the electron-beam power density must be below a maximum value. This value is somewhere in the range 0.4-0.8 W/µm depending on the anode material.[2] This means that a solid-anode microfocus source with a 10 µm electron-beam focus can operate at a power in the range 4-8 W.
In metal-jet-anode microfocus X-ray tubes the solid metal anode is replaced with a jet of liquid metal, which acts as the electron-beam target. The advantage of the metal-jet anode is that the maximum electron-beam power density is significantly increased. Values in the range 3-6 W/µm have been reported for different anode materials (gallium and tin).[3][4] In the case with a 10 µm electron-beam focus a metal-jet-anode microfocus X-ray source may operate at 30-60 W.
The major benefit of the increased power density level for the metal-jet X-ray tube is the possibility to operate with a smaller focal spot, say 5 µm, to increase image resolution and at the same time acquire the image faster, since the power is higher (15-30 W) than for solid-anode tubes with 10 µm focal spots.
Physics
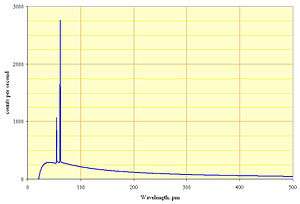
As with any vacuum tube, there is a cathode, which emits electrons into the vacuum and an anode to collect the electrons, thus establishing a flow of electrical current, known as the beam, through the tube. A high voltage power source, for example 30 to 150 kilovolts (kV), is connected across cathode and anode to accelerate the electrons. The X-ray spectrum depends on the anode material and the accelerating voltage.[5]
In many applications, the current flow (typically in the range 1 mA to 1 A) is able to be pulsed on for between about 1 ms to 1 s. This enables consistent doses of X-rays, and taking snapshots of motion. Until the late 1980s, X-ray generators were merely high-voltage, AC to DC variable power supplies. In the late 1980s a different method of control was emerging, called high speed switching. This followed the electronics technology of switching power supplies (aka switch mode power supply), and allowed for more accurate control of the X-ray unit, higher quality results, and reduced X-ray exposures.
Electrons from the cathode collide with the anode material, usually tungsten, molybdenum or copper, and accelerate other electrons, ions and nuclei within the anode material. About 1% of the energy generated is emitted/radiated, usually perpendicular to the path of the electron beam, as X-rays. The rest of the energy is released as heat. Over time, tungsten will be deposited from the target onto the interior surface of the tube, including the glass surface. This will slowly darken the tube and was thought to degrade the quality of the X-ray beam, but research has suggested there is no effect.[6] Eventually, the tungsten deposit may become sufficiently conductive that at high enough voltages, arcing occurs. The arc will jump from the cathode to the tungsten deposit, and then to the anode. This arcing causes an effect called "crazing" on the interior glass of the X-ray window. As time goes on, the tube becomes unstable even at lower voltages, and must be replaced. At this point, the tube assembly (also called the "tube head") is removed from the X-ray system, and replaced with a new tube assembly. The old tube assembly is shipped to a company that reloads it with a new X-ray tube.
The X-ray photon-generating effect is generally called the bremsstrahlung effect, a contraction of the German bremsen for braking, and strahlung for radiation.
The range of photonic energies emitted by the system can be adjusted by changing the applied voltage, and installing aluminum filters of varying thicknesses. Aluminum filters are installed in the path of the X-ray beam to remove "soft" (non-penetrating) radiation. The number of emitted X-ray photons, or dose, are adjusted by controlling the current flow and exposure time.
The tube current and exposure time affect the dose and therefore the contrast of the image.
Heat unit
Since the introduction of scattered electron traps, directly cooled liquid metal anode bearings, rotating frame tubes and other modern technology the term has become misleading when used for the objective comparison of the performance of medical rotating anode X-ray tubes. Accordingly, the IEC 60613 standard has been revised in 2010. Anode heat storage capacity and implicitly "Heat Units" were abandoned and replaced by terms of practical relevance, e.g. NOMINAL CT ANODE INPUT POWER. Historically, heat units were referring to the amount of heat stored in a solely radiation cooled anode inside an electron reflecting glass envelope. In radiography, in particular in radiology, a heat unit was a usual unit derived from the Joule and measuring the quantity of heat in a device, in particular the thermal energy that an X-ray tube must be able to support and dissipate during and after an exam.
Historically, this unit comes from the need to express a quantity of energy whatever the waveform of the electrical source power (direct or pulsating). The heat produced in these devices is (in Joule) :
In radiography voltage is usually expressed in (thousands of volts peak), the effective current in mA and the time in seconds:
w being the waveform ratio. With a full-wave rectification of a sine wave it equals , thus the practical unit:
- 1 HU = 0.707 J or
- 1.4 HU = 1 J [7]
History
Crookes tube
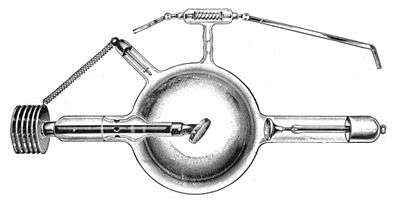
Historically, X-rays were discovered radiating from experimental discharge tubes called Crookes tubes invented by British physicist William Crookes and others. As the medical and other uses of X-rays became apparent, workshops began to manufacture specialized Crookes tubes to produce X-rays. These were the first X-ray tubes. These first generation cold cathode or Crookes X-ray tubes were used until the 1920s.
Crookes tubes generated the electrons needed to create X-rays by ionization of the residual air in the tube, instead of a heated filament, so they were partially but not completely evacuated. They consisted of a glass bulb with around 10−6 to 5×10−8 atmospheric pressure of air (0.1 to 0.005 Pa). An aluminum cathode plate at one end of the tube created a beam of electrons, which struck a platinum anode target at the center generating X-rays. The anode surface was angled so that the X-rays would radiate through the side of the tube. The cathode was concave so that the electrons were focused on a small (~1 mm) spot on the anode, approximating a point source of X-rays, which resulted in sharper images. The tube had a third electrode, an anticathode connected to the anode. It improved the X-ray output, but the method by which it achieved this is not understood. A more common arrangement used a copper plate anticathode (similar in construction to the cathode) in line with the anode such that the anode was between the cathode and the anticathode.
To operate, a DC voltage of a few kilovolts to as much as 100 kV was applied between the anodes and the cathode, usually generated by an induction coil, or for larger tubes, an electrostatic machine. This created and then accelerated a small number of ions from the low pressure gas in the tube. These struck further gas atoms, knocking electrons off them, creating more positive ions in a chain reaction. All the positive ions were attracted to the cathode. When they struck it, they knocked electrons out of the metal, which were accelerated along with the electrons knocked from the gas atoms toward the anode target. When these high speed electrons struck the atoms of the anode, they created X-rays by one of two processes, either Bremsstrahlung or X-ray fluorescence.
Crookes tubes were unreliable. As time passed, the residual air would be absorbed by the walls of the tube, reducing the pressure. This increased the voltage across the tube, generating 'harder' X-rays, until eventually the tube stopped working. To prevent this, 'softener' devices were used (see picture). A small tube attached to the side of the main tube contained a mica sleeve or chemical that released a small amount of gas when heated, restoring the correct pressure.
The glass envelope of the tube would blacken in use due to the X-rays affecting its structure.
Coolidge tube
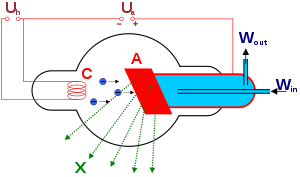
- C: filament/cathode (-)
- A: anode (+)
- Win and Wout: water inlet and outlet of the cooling device
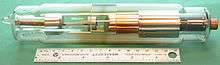
The Crookes tube was improved by William Coolidge in 1913.[8] The Coolidge tube, also called hot cathode tube, is the most widely used. It works with a very good quality vacuum (about 10−4 Pa, or 10−6 Torr).
In the Coolidge tube, the electrons are produced by thermionic effect from a tungsten filament heated by an electric current. The filament is the cathode of the tube. The high voltage potential is between the cathode and the anode, the electrons are thus accelerated, and then hit the anode.
There are two designs: end-window tubes and side-window tubes. End window tubes usually have "transmission target" which is thin enough to allow X-rays to pass through the target (X-rays are emitted in the same direction as the electrons are moving.) In one common type of end-window tube, the filament is around the anode ("annular" or ring-shaped), the electrons have a curved path (half of a toroid).
What is special about side-window tubes is an electrostatic lens is used to focus the beam onto a very small spot on the anode. The anode is specially designed to dissipate the heat and wear resulting from this intense focused barrage of electrons. Some anodes are mechanically spun to increase the area heated by the beam (e.g. edical "rotating anode") or cooled by circulating coolant (indirectly on most rotating anodes). The anode is precisely angled at 1-20 degrees off perpendicular to the electron current so as to allow the escape of some of the X-ray photons which are emitted perpendicular to the direction of the electron current. The anode is usually made out of tungsten or molybdenum. The tube has a window designed for escape of the generated X-ray photons.
The power of a Coolidge tube usually ranges from 0.1 to 18 kW.
Hazards of X-ray production from vacuum tubes

Any vacuum tube operating at several thousand volts or more can produce X-rays as an unwanted byproduct, raising safety issues.[9][10] The higher the voltage, the more penetrating the resulting radiation and the more the hazard. CRT displays, once common in color televisions and computer displays, operate at 3-40 kilovolts,[11] making them the main concern among household appliances. Historically, concern has focused less on the cathode ray tube, since its thick glass envelope is impregnated with several pounds of lead for shielding, than on high voltage (HV) rectifier and voltage regulator tubes inside. In the late 1960s it was found that a failure in the HV supply circuit of some General Electric TVs could leave excessive voltages on the regulator tube, causing it to emit X-rays. The models were recalled and the ensuing scandal caused the US agency responsible for regulating this hazard, the Center for Devices and Radiological Health of the Food and Drug Administration (FDA), to require that all TVs include circuits to prevent excessive voltages in the event of failure. The hazard associated with excessive voltages was eliminated with the advent of all solid state TVs, which have no tubes beside the CRT. Since 1969 the FDA has limited TV X-ray emission to 0.5 mR (milliroentgen) per hour. The flat screens used today do not have any vacuum tubes capable of emitting X-rays.
See also
![]() |
Wikimedia Commons has media related to X-ray tubes. |
- Electron beam tomography
- Coronary angiography
- Synchrotron radiation
- X-ray fluorescence
- X-ray generator
- glass-to-metal-seal
Patents
- Coolidge, U.S. Patent 1,211,092, "X-ray tube"
- Langmuir, U.S. Patent 1,251,388, "Method of and apparatus for controlling X-ray tubes
- Coolidge, U.S. Patent 1,917,099, "X-ray tube"
- Coolidge, U.S. Patent 1,946,312, "X-ray tube"
References
- ↑ Behling, Rolf (2015). Modern Diagnostic X-Ray Sources, Technology, Manufacturing, Reliability. Boca Raton, FL, USA: Taylor and Francis, CRC Press. ISBN 9781482241327.
- ↑ D. E. Grider, A Wright, and P. K. Ausburn (1986), “Electron beam melting in microfocus x-ray tubes”, J. Phys. D: Appl. Phys. 19: 2281-2292
- ↑ M. Otendal, T. Tuohimaa, U. Vogt, and H. M. Hertz (2008), “A 9 keV electron-impact liquid-gallium-jet x-ray source”, Rev. Sci. Instrum. 79: 016102
- ↑ T. Tuohimaa, M. Otendal, and H. M. Hertz (2007), “Phase-contrast x-ray imaging with a liquid-metal-jet-anode microfocus source”, Appl. Phys. Lett. 91: 074104
- ↑ Diagram of continuum and characteristic lines Archived February 23, 2008, at the Wayback Machine.
- ↑ John G. Stears; Joel P. Felmlee; Joel E. Gray (September 1986), "cf., Half-Value-Layer Increase Owing to Tungsten Buildup in the X-ray Tube: Fact or Fiction", Radiology, 160 (3): 837–838, doi:10.1148/radiology.160.3.3737925
- ↑ Perry Sprawls, Ph.D. X-Ray Tube Heating and Cooling, from The web-based edition of The Physical Principles of Medical Imaging, 2nd Ed.
- ↑ Coolidge, U.S. Patent 1,203,495. Priority date May 9, 1913.
- ↑ "We want you to know about television radiation". Center for Devices and Radiological Health, US FDA. 2006. Archived from the original on December 18, 2007. Retrieved 2007-12-24.
- ↑ Pickering, Martin. "An informal history of X-ray protection". sci.electronics.repair FAQ. Retrieved 2007-12-24.
- ↑ Hong, Michelle. "Voltage of a Television Picture Tube". Retrieved 11 August 2016.
External links
- X-ray Tube - A Radiograph of an X-ray Tube
- The Cathode Ray Tube site
- NY State Society of Radiologic Sciences
- Collection of X-ray tubes by Grzegorz Jezierski of Poland
- Excillum AB, a manufacturer of metal-jet-anode microfocus x-ray tubes
- example of how X-ray tubes work.