Electroforming
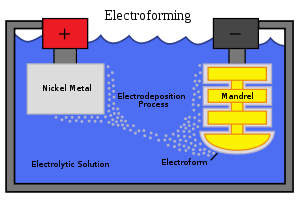
Electroforming is a metal forming process that forms parts through electrodeposition or electroplating on a model, known in the industry as a mandrel. Conductive (metallic) mandrels are pre-treated chemically to allow subsequent separation of the finished electroform, non-conductive (glass, silicon, plastic) mandrels require the deposition of a conductive layer. Conductive layers can be deposited chemically, or using vacuum deposition techniques. The outer surface of the mandrel forms the inner surface of the form. A thick layer of electroplating is applied until the plate itself is strong enough to be self-supporting. The mandrel is most often separated intact or dissolved away after forming, but occasionally (as in the case in decorative electroforming) left in place. The surface of the finished part that was in intimate contact with the mandrel is rendered in fine detail with respect to the original, and is not subject to the shrinkage that would normally be experienced in a foundry cast metal object, or the tool marks of a milled part. The side of the part that was in contact with the plating solution is less well defined, and that loss of definition increases with thickness of plating. In extreme cases, where a thickness of several millimetres is required, there is preferential build-up of material on sharp outside edges and corners. This tendency can be reduced by a process known as periodic reverse,[1] where the plating current is reversed for short periods during electroforming and the excess is preferentially etched away. The finished plated form can either be the finished part, or can be used in a subsequent process to produce a positive of the original mandrel shape.
In recent years, due to its ability to replicate a mandrel surface very precisely with practically no loss of fidelity, electroforming has taken on new importance in the fabrication of micro and nano scale metallic devices and in producing precision injection moulds with micro and nano scale features for production of non-metallic micro-moulded objects.
Process
In the basic electroforming process, an electrolytic bath is used to deposit nickel or other electroformable metals onto a conductive patterned surface, such as stainless steel. Once the deposited material has been built up to the desired thickness, the master electroform is parted from the premaster substrate. This process allows high-quality duplication of the premaster and therefore permits quality production—at low unit costs with high repeatability and excellent process control.
If the mandrel is made of a non-conductive material it can be covered with a conductive coating. Technically, it is a process of synthesizing a metal object by controlling the electrodeposition of metal passing through an electrolytic solution onto a metal or metalized form.
The object being electroformed can be a permanent part of the end product or can be temporary (as in the case of wax), and removed later, leaving only the metal form, the “electroform”. New technologies have made it possible for mandrels to be very complex. In order to facilitate the removal of the electroform from the mandrel, a mandrel is often made of aluminum. Because aluminum can easily be chemically dissolved, a complex electroform can be produced with near exactness.
Advantages and disadvantages
The main advantage of electroforming is that it reproduces the external shape of the mandrel within one micrometre. Generally, forming an internal cavity accurately is more difficult than forming an external shape, however the opposite holds true for electroforming because the mandrel's exterior can be accurately machined.[2]
Compared to other basic metal forming processes (casting, forging, stamping, deep drawing, machining and fabricating) electroforming is very effective when requirements call for extreme tolerances, complexity or light weight. The precision and resolution inherent in the photographically produced conductive patterned substrate, allows finer geometries to be produced to tighter tolerances while maintaining superior edge definition with a near optical finish. Electroformed metal is extremely pure, with superior properties over wrought metal due to its refined crystal structure. Multiple layers of electroformed metal can be molecularly bonded together, or to different substrate materials to produce complex structures with "grown-on" flanges and bosses.
Tolerances of 1.5 to 3 nanometres have been reported.
A wide variety of shapes and sizes can be made by electroforming, the principal limitation being the need to part the product from the mandrel. Since the fabrication of a product requires only a single pattern or mandrel, low production quantities can be made economically.
See also
References
- ↑ Journal of Applied Electrochemistry 1979 407-410 Periodic reverse current electroplating and surface finishing. M.I. Ismail
- ↑ The electroforming process, archived from the original on 2010-02-02, retrieved 2010-02-02.
Further reading
- Spiro, P. Electroforming: A comprehensive survey of theory, practice and commercial applications, London, 1971.
External links
- Electroforming process video
- "Opti-Forms, Inc. - Optical Coatings, Electroformed Reflectors, Cold Shields". Opti-Forms, Inc. Retrieved 2015-08-28.
- "Engility :: Home". www.drc.com. Retrieved 2015-08-28.
- NiCoForm, Inc. "Net-shape Electroforming". www.nicoform.com. Retrieved 2015-08-28.